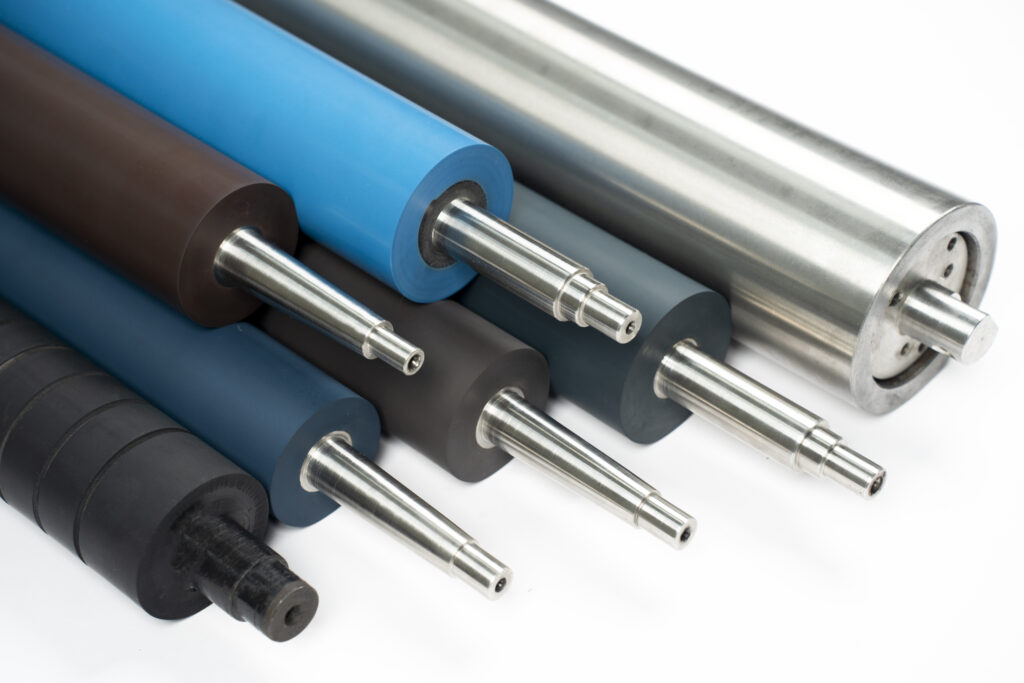
When it comes to complex processes like Offset Printing that involve multiple moving parts, the adage “the God is in the details” is particularly true.
One such detail that often goes unnoticed, but plays a pivotal role in the efficiency and the final output of the print quality, is the material of the Rubber Rollers.
At first glance, Rubber Rollers may seem like any other component of the printing press, but their role is far from ordinary. Rubber Rollers are the unsung heroes that efficiently transfer the ink from the fountain to the printing plate.
The quality of this ink transfer, which is fundamental to the print’s final quality, is significantly influenced by the type of material used in the roller.
In this blog post, let’s deep dive into the importance of material selection for Rubber Rollers and how it affects not just the print output but also the longevity of the Rollers themselves.
Material Selection for Rubber Rollers
Rubber Rollers are commonly composed of various synthetic materials, like Nitrile, EPDM, Silicone, and Polyurethane, amongst others.
Each of these materials have unique properties that makes them suitable for diverse printing applications. For instance, Nitrile is renowned for its excellent oil resistance which makes it ideal for oil-based ink printing jobs.
On the other hand, EPDM’s excellent chemical resistance properties makes it perfect for outdoor printing or processes that use very strong cleaning solvents.
Impact on the Offset Printing Process
The material of the Rubber Roller can significantly impact the printing process.
For example, the hardness of the Rubber, which can vary based on the material, affects how well the ink is transferred from the roller to the plate. If the Rubber is too soft, the ink may not distribute evenly. Contrastingly, if the Rubber is too hard, the ink may not transfer efficiently.
The heat resistance of the Rubber material also plays an important role, especially in processes such as heat-set Web Offset Printing where the Rollers must withstand high temperatures. In such cases, materials like Silicone, known for their excellent heat resistance, become the perfect fit.
Roller Longevity and Material Selection
The material of the Roller is also closely linked to its lifespan. Certain materials resist wear and tear, oils, and chemicals better than others, translating into longer Roller life.
For instance, Rollers made from Polyurethane are known for their exceptional durability and resistance to abrasion which gives them a longer lifespan compared to the Rollers made from other materials.
Choosing The Right Material
Material selection in Rubber Rollers isn’t a one-size-fits-all process but one that warrants a careful consideration that depends on your specific printing needs, types of inks used, and the prevalent operating conditions of your printing press.
It is pertinent to note that choosing the right material for your Rubber Rollers isn’t just about enhancing the print quality but equally about improving your printing press’s efficiency by minimising the regular downtimes due to frequent Roller replacements.
Understanding the unique properties of each material and aligning them with your specific printing needs is crucial to ensure that your Rubber Rollers contribute positively to your Offset Printing process.
As India’s leading Rubber Rollers manufacturer, leading Offset Printing companies across the country trust Stellar’s expertise to choose the right Roller for their printing press.
With a comprehensive portfolio of high-quality Rubber Rollers that are specifically customised to suit your exact printing needs, Stellar handholds you at every step of the Roller selection process.
To learn how Stellar’s Rubber Rollers can help you get a superior print quality as well as make a cost-effective decision that can extend your Rollers’ life, reduce downtime, and improve your printing operation’s overall productivity, please visit https://stellarrubberrollers.com or get in touch with us at contact@stellarrubberrollers.com.